Bits and Pieces
“There are many in this old world of ours who hold that things break about even for all of us. I have observed, for example, that we all get the same amount of ice. The rich get it in the summertime and the poor get it in the winter.”
– Bartholemew William Barclay Masterson 1853-1921 Sherrif, Gunfighter, Gambler, Newspaper Reporter, and friend of President Theodore Roosevelt
Power of the Future
In 1939, the U.S. Navy Research Laboratory began exploring the construction of a nuclear-powered submarine. By 1955, the USS Nautilus was at sea. Soon after, the USSR introduced the commercial cargo ship Lenin, followed by the U.S. launching the Savannah in 1959.
With a few exceptions – Germany’s NS Otto Hahn (1964) and Japan’s NS Mutsu (1969) – the world went to nuclear powered war ships. Russia, however, occupied a unique middle ground with a fleet of nuclear-powered icebreakers.
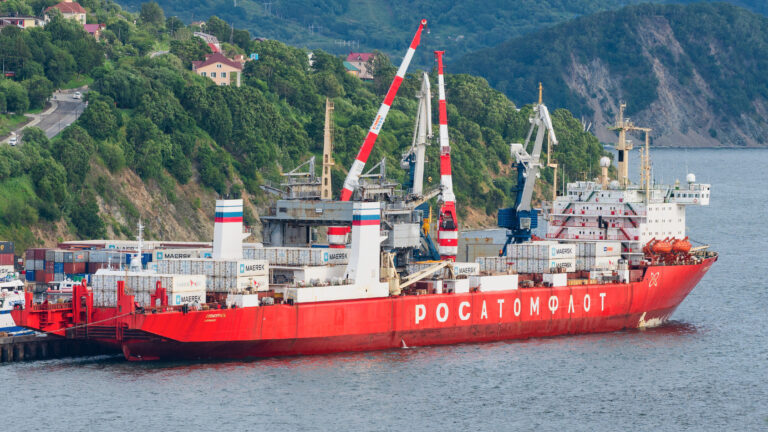
Now, several countries are looking into the use of nuclear propulsion for commercial vessels to replace petroleum-based fuels that emit greenhouse gases. Nuclear systems not only eliminate the need for regular refueling in ports worldwide, but also reduce downtime, maintenance, and the costs associated with diesel engines. Nuclear ships could potentially go 10 years between refueling.
The current nuclear power system used on board vessels is quite different than what is found in land nuclear plants. The normal system has nuclear fusion heating water that is kept under pressure and not boiling. Despite its operating temperature of 432-572 F or as originally known 250-500 degrees centigrade. This hot water in turn heats an adjacent water system that turns to steam which powers a turbine. In many cases the turbine drives the vessel directly through a gear system. For the vessels of France and China, the turbine powers generators whose electricity powers a propulsion system.
Doing this on board a vessel is much more difficult than this system on shore. Because of the confined space, a small modular reactor (SMR) is needed. A reactor in a small, confined space must produce as much power as possible under rough external and internal conditions, including vibration, under very difficult maintenance conditions and a more highly enriched uranium, and scheduling eventual refueling at rare sites. There are even difficulties in this onboard system.
The new type of nuclear-powered engine, also very suitable for vessels, is the sodium-cooled fast reactor (SFR). This is in active development in Russia, Japan, India, China, France, and the U.S., with support from companies in the U.K. and elsewhere. An upcoming edition may dive deeper into SFRs and their potential to fully transition shipping away from petroleum, coal, and even current “green” dual-fuel systems.
Insurance, Regulation, and Risk
What is interesting is the current and future planning of those who allow ships to operate. It is a growing cost to them. It is the thinking and planning of insurance underwriters. Things that will have to be agreed upon by the providers of insurance and their users are already complicated but will have to take very difficult steps as the marine industry over the next decade moves toward new nuclear power systems. These are already the plans and agreements being worked on between the insurers and owners/operators of the now comparatively current simple vessels. These are those now powered by bi-fuels, sails, or those operated by a “Captain” many miles away.
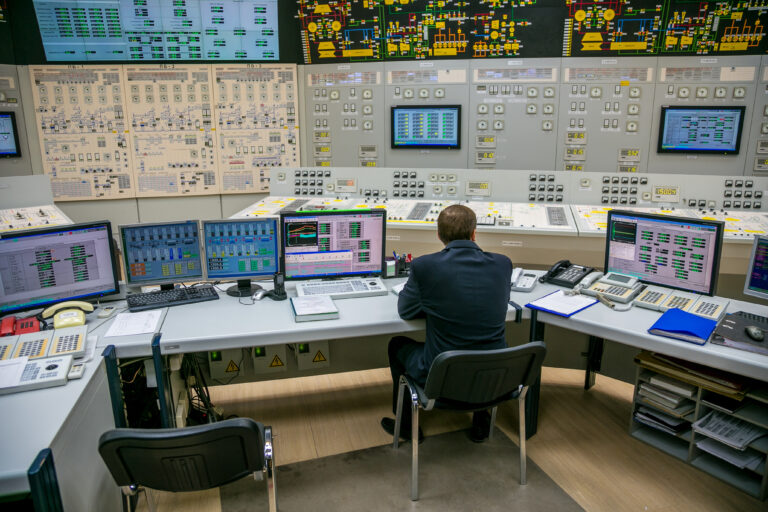
The future use of nuclear commercial vessels involves many steps by underwriters, builders, operators, and charterers. Such steps are currently being taken to insure new larger and more scientifically complicated “Green” ships, their cargoes, and their more complicated operations. While some insurance coverage for nuclear power sources already exists, additional measures will be needed as nuclear technology becomes more common in commercial shipping.
Floating nuclear power plants already exist – most notably in Russia, where barges moored near land serve as mobile reactors. The Russian Register of Shipping (formerly under the USSR) established safety and maintenance regulations for floating vessels as far back as the 1950s.
Any shipyard building a nuclear vessel will need an Emergency Planning Zone (EPZ). These are safety zones around current nuclear power plants with high-pressure nuclear reactors. Insurance is required, not just to cover physical damage but also the effects of potential contamination. During ship construction at an approved EPZ site, the same liability coverage required at standard sites must be in place – specifically, coverage for the arrival of nuclear fuel and while it is being loaded into the ship’s reactor. Once the fuel is loaded, the vessel can be insured as a complete ship. However, there may be a separate, full-ship policy that takes effect once the ship leaves the shipyard and is no longer covered under the shipyard’s policy. Additionally, it’s important to clarify whether this new policy will cover both the ship and its cargo.
In the U.S., there is already a commercial nuclear risk insurance pool with over $34 billion in coverage. Beyond that, government-owned or military-affiliated plants are covered under separate systems. Going forward, new pools may be needed – covering ships under construction, operational vessels, crews, cargo, and potential incidents requiring salvage or decontamination and the possible legal spread of “perils”.
Back in 1962, the International Maritime Organization (IMO) drafted the Convention on the Liability of Operators of Nuclear Ships. Unfortunately, it was never ratified. Now, the IMO – along with the International Association of Classification Societies (IACS) – will need to revisit and modernize standards for the safe operation of nuclear-powered ships.
Early groundwork is already being laid by classification societies such as RS and Lloyd’s Register, with training and regulatory involvement expanding through ABS, Bureau Veritas, and DNV.
Inland
Recent reports on inland shipping trends don’t require extensive detail. Commodity movement has remained relatively stable overall, with some decline in materials like cement and salt. Grain flows – especially corn moving south – are holding up well, keeping hopper barge rates strong, despite natural river fluctuations.
The Mississippi River continues to play its part: shallow waters north of St. Louis and high waters farther south impact barge operations and delivery efficiency. Still, in 2024, the construction of new hopper barges has edged upward compared to 2023 – though it’s not back to peak levels from earlier in the decade.
In 2024, a total of 395 jumbo hopper barges were delivered, marking an increase from the 340 barges delivered in 2023.
The cost of steel remains a major factor:
- 2023 average: $1,495 per short ton
- 2024 average (so far): $1,195 per short ton
- Q4 2024: $1,039 — the lowest since early 2021
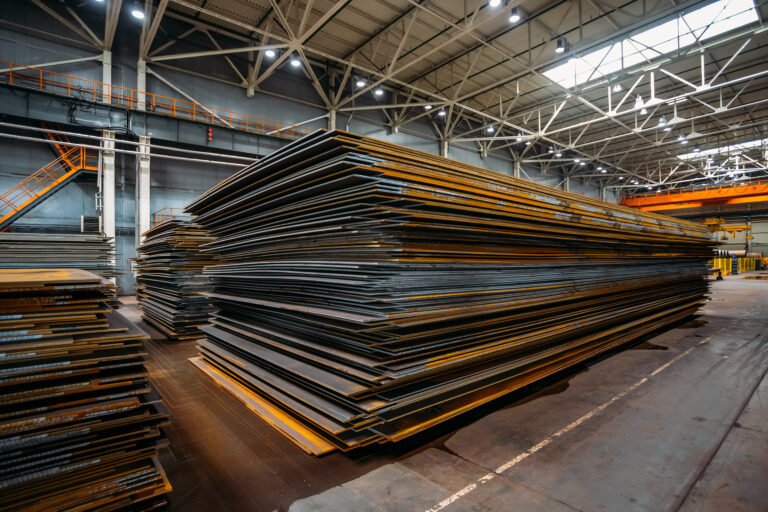
In 2024, eleven entities bought barges, up from ten in 2023. Of interest is that several of the buyers have purchased to lease to others. MKJ is known as a barge chartering company. CIBCO is a portion of the well-known shipyard C&C Marine. The following data is from River Transport News:
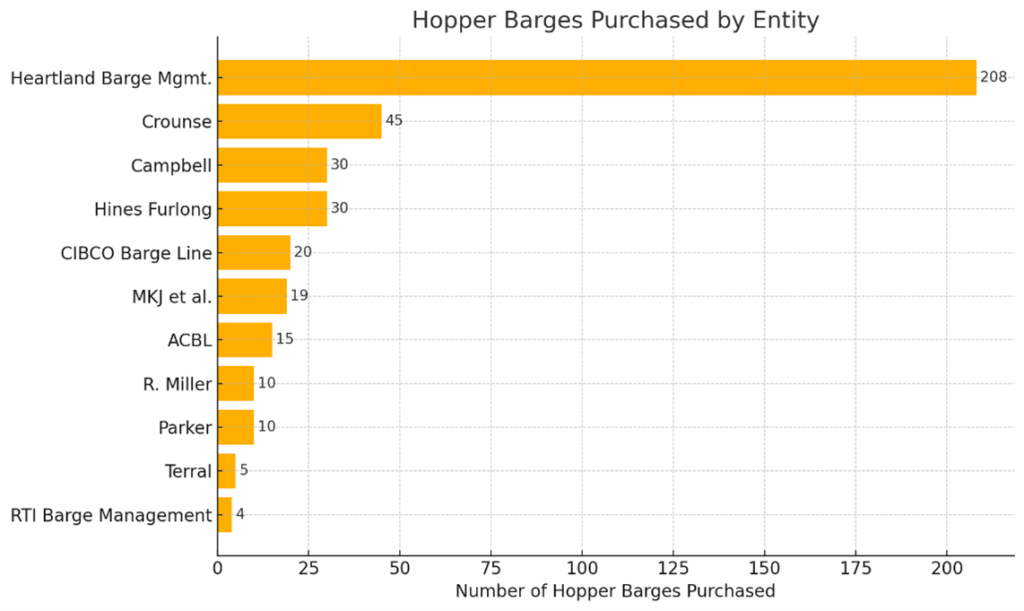
Most of these barges were covered hoppers built by Arcosa.
It’s worth noting that 145 hopper barges will be scrapped or repurposed in 2025. Aging barges are increasingly being extended through major maintenance – including full re-plating – which, while costly, is still often cheaper than new builds under U.S. steel prices.
International trade is already under some changes due to the plans and decisions of numerous countries. This graph from www.econovis.net shows trends that will have effects on domestic inland and coastal trade in many countries including the United States.
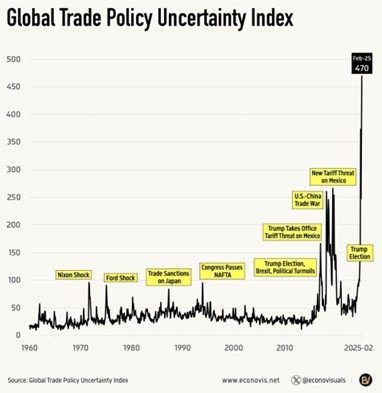
Flag State Inspectors, Class Surveyors, USCG, Insurance Inspections – and AI
Artificial Intelligence is becoming more widely recognized in the marine industry, especially for its potential to reduce costs and improve reliability.
One key application: predictive maintenance. Traditionally, vessels operate under fixed inspection intervals – annual, five-year, ten-year, etc. But real-world wear and tear doesn’t always follow the calendar. There’s the risk of under-maintenance, when a failure occurs before a scheduled inspection, and over-maintenance, when parts are replaced prematurely. AI-powered analytics and cloud-based fleet management platforms are changing that. With data from ship sensors, owners can shift from calendar-based overhauls to Condition-Based Maintenance (CBM) and Data Condition Based Maintenance (DCBM) – replacing parts when needed, not just when scheduled. This benefits profitability and safety – but presents challenges for regulatory bodies and inspection regimes.
Large propulsion and generator engines have provided remote engine condition data for many years. The classification group Lloyd’s Register has started working in a system with several large shipping companies.
The next step? Integration among vessel owners, shipyards, equipment manufacturers, and regulatory inspection bodies – building a system where digital tools and traditional inspections complement each other.
-Norm Laskay
If you’d like to keep this conversation going, email me at NLaskay@DLSmarine.com